IMET and REEF Alum Pivots to Produce Face Shields
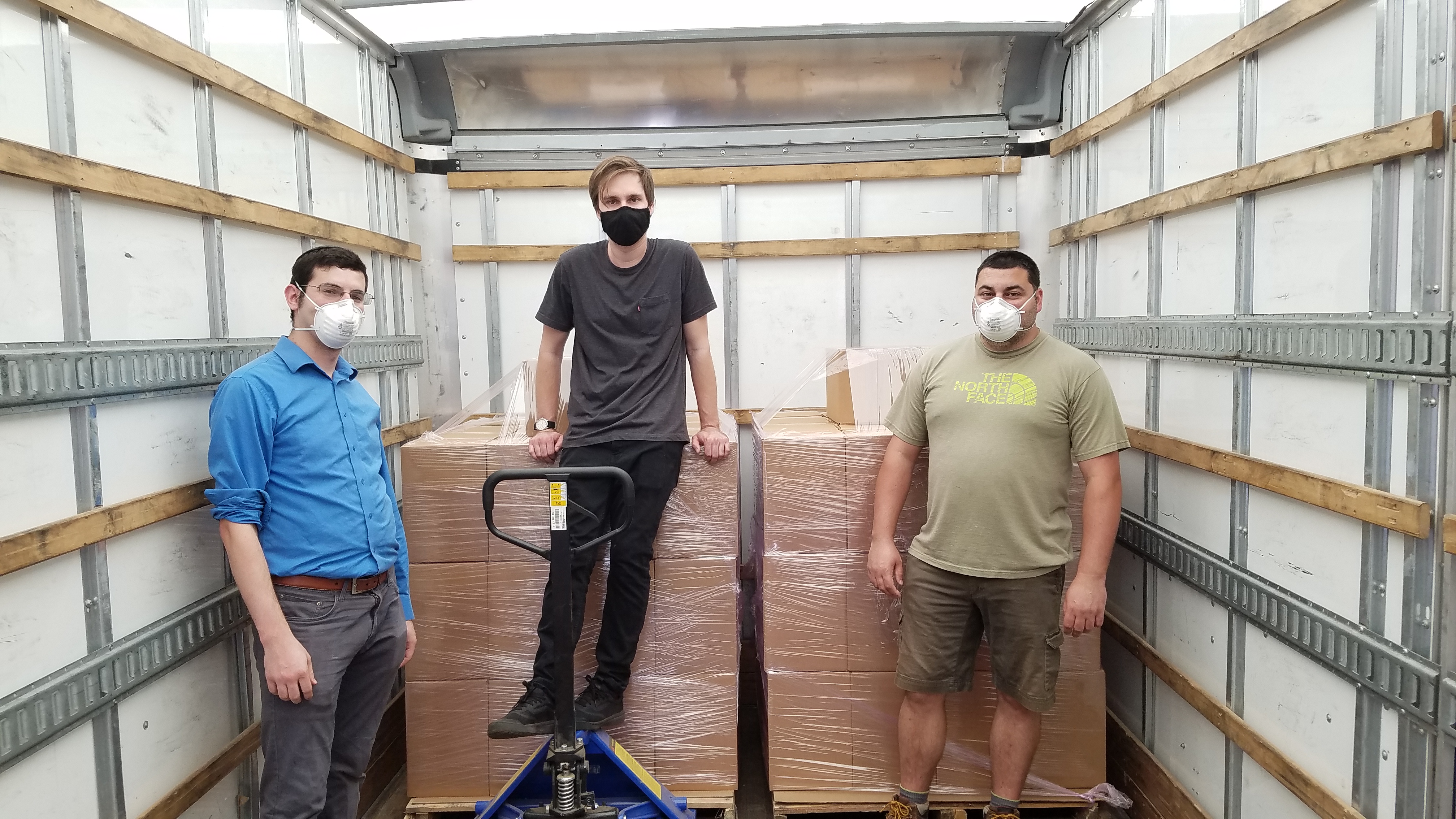
Find Manta Biofuel on LinkedIn
Manta Biofuel typically conducts research and development for algal biofuels, but these days, a small team is churning out 6,500 face shields each week for health care workers, hairdressers, electricians, and our IMET scientists. The company’s co-founder, Dr. Ryan Powell, is an IMET and REEF alum who knows how to harness an opportunity when he sees it. At a time when unemployment numbers are looking bleak, he kept his whole team employed and brought on two additional employees to help keep up with demand. As the enormity of this pandemic set in, he said, “We thought what can we do to help? What can we do to try to bring some money through the front door?” They had a machine for cutting plastics, skilled engineers, and experience applying for grants, all of which helped them quickly pivot to a new focus that could help keep people safe.
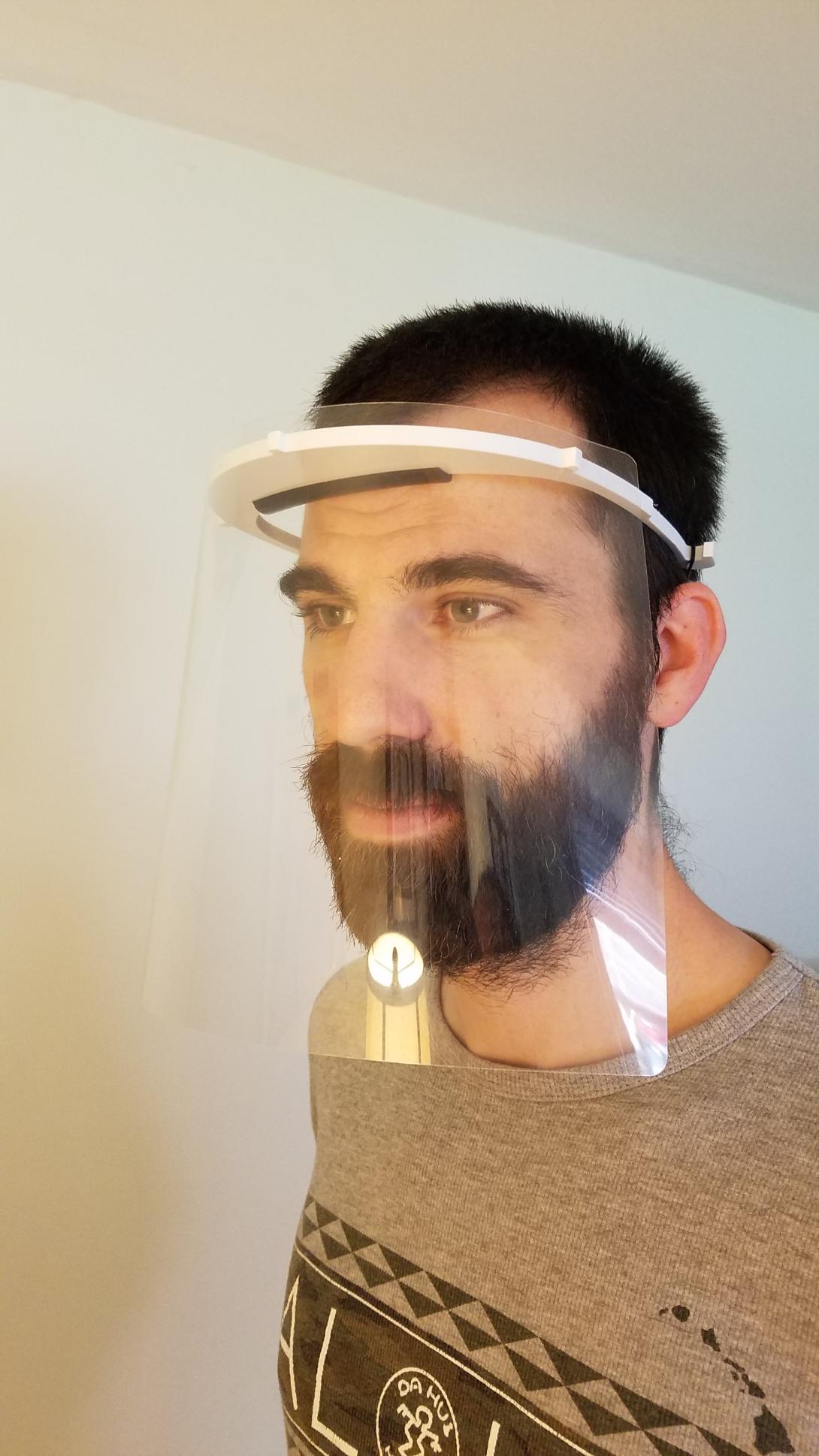
John Sturgis, Manta’s Lead Engineer, quickly began designing a prototype of a face shield, working many long days to ensure the design provided appropriate protection, was comfortable, and could be made quickly and cheaply. These shields have a plastic visor that goes around the head with foam padding for comfort and a plastic sheet that extends down to cover the nose and mouth. They are meant to be used in combination with a face mask, to extend the mask’s life. A plastic cutting machine, which Manta typically uses to design prototypes for harvesting algae, cuts the visor from a sheet of plastic. In the first iteration of the design, they could sell the shields for $15-20 per unit. John Sturgis further refined the design and manufacturing process so that Manta can now offer them at a very competitive price of $2.00 per unit.
The most time-consuming part of the manufacturing process is cutting the visor and so the machine, a router table, is now running nearly constantly. Only one person is in the facility at a time, with shifts running throughout the day. When I spoke with Ryan, he had just gotten off his daily 5:30-7:00 am shift. Two additional employees, both of whom had been put out of work by the pandemic, were brought on to help with production.
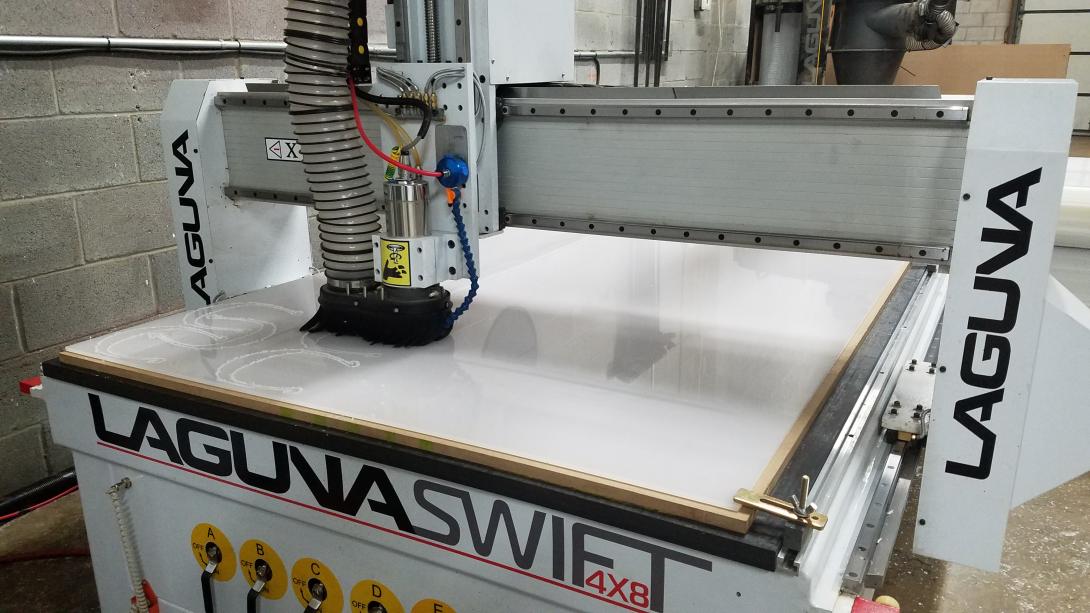
Manta’s quick pivot was helped along by a grant from the State of Maryland, which provided funds for initial purchases of supplies. As part of this grant, they are encouraged to sell to companies in Maryland. They have already sold face shields to the Montgomery County government and local distributors. They also recently donated 100 face shields to IMET, where a small number of researchers are returning to their labs to continue experiments. Word has traveled about Manta Biofuel’s face shields and they have been contacted about orders on the scale of one million units. While their current machinery would not support producing that volume, Ryan said that they are considering whether to partner with other companies with advanced equipment to do so. With a team that is accustomed to designing novel devices for research and development, they have all the necessary engineering expertise, and the profit from such an expansion might help them fund biofuel development in the future.
While the focus of the last few months has been on manufacturing face shields, Manta Biofuel continues to advance its mission of creating carbon-neutral and cost-competitive biofuels; it just looks different this year. During most years, they would be growing and harvesting algae at this time, but they have essentially lost this production season. Instead, Ryan is using this time to focus on meeting potential investors, who have continued to show interest in Manta’s technology. The team has also learned some new skills from their quick pivot, gaining experience in production, supply chain management, and sales. These skills may help them as Manta grows in the future, but that wasn’t a major motivation for shifting to producing face shields. When it comes down to it, Ryan said, “We’re just happy to be able to do something to help.”
This article was first published in the quarterly IMET newsletter, "Inside IMET." Be the first to hear updates from IMET by signing up for our mailing list.